The main uses and application areas of magnesia carbon bricks include the following aspects:
Steelmaking converter: Magnesia carbon bricks are widely used in steelmaking converters, mainly in furnace mouths, furnace caps and charging sides. The use conditions of various parts of the converter working lining are different, so the use effects of magnesia carbon bricks are also different. The furnace mouth needs to be resistant to the scouring of high-temperature slag and high-temperature exhaust gas, not easy to hang steel and easy to clean; the furnace cap is subject to severe slag erosion and rapid cooling and heating temperature changes, and requires magnesia carbon bricks with strong slag erosion resistance and spalling resistance; the charging side requires magnesia carbon bricks with high strength and spalling resistance.
Electric furnace: In electric furnaces, the furnace walls are almost all built with magnesia carbon bricks. The quality of magnesia carbon bricks for electric furnaces depends on the purity of the MgO source, the type of impurities, the grain bonding state and size, and the purity and crystallization degree of flake graphite. Adding antioxidants can improve the performance of magnesia carbon bricks, but it is not necessary under normal operating conditions. Metal antioxidants are only needed in electric arc furnaces with high FeOn slag.
Ladle: Magnesia carbon bricks are also used in the slag line of the ladle. These parts are severely eroded by slag and require magnesia carbon bricks with excellent slag erosion resistance. Magnesia carbon bricks with higher carbon content are usually more effective.
Other high-temperature applications: Magnesia carbon bricks are also used in basic steelmaking open-hearth furnaces, electric furnace bottoms and walls, permanent linings of oxygen converters, non-ferrous metal smelting furnaces, high-temperature tunnel kilns, calcined magnesia bricks and cement rotary kiln linings, as well as the bottoms and walls of heating furnaces.
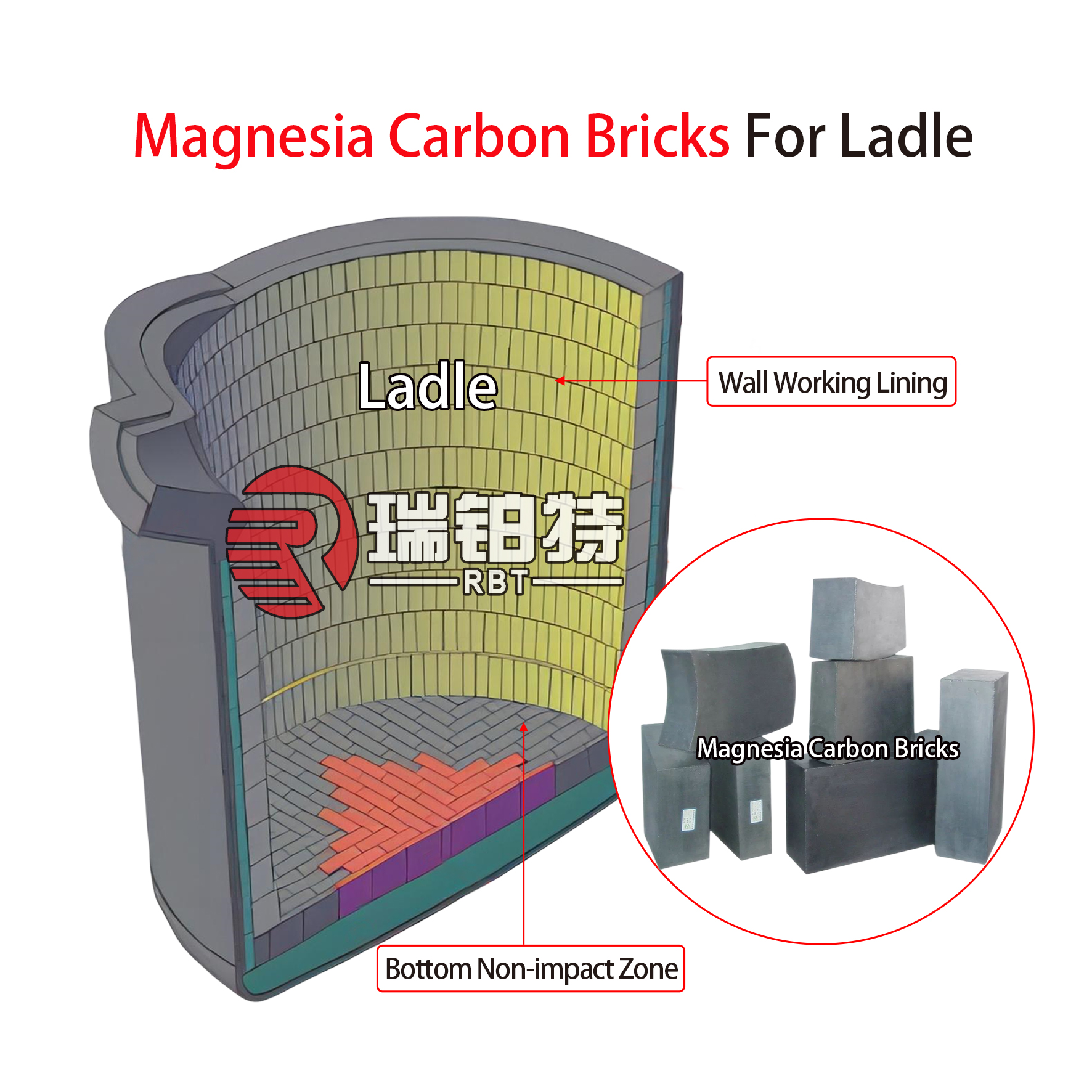
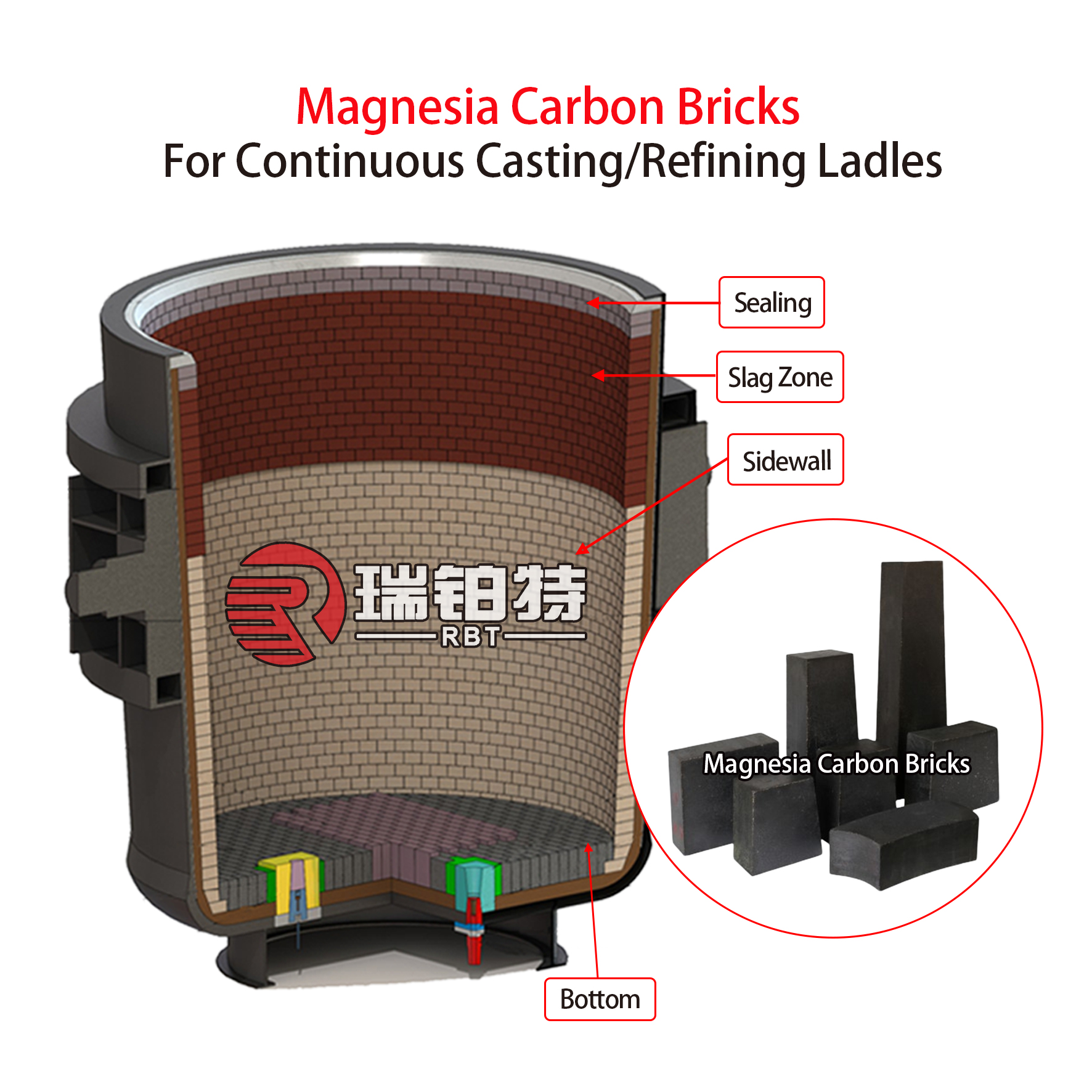
Post time: May-15-2025