The reasons for cracks in castables during baking are relatively complex, involving heating rate, material quality, construction technology and other aspects. The following is a specific analysis of the reasons and corresponding solutions:
1. Heating rate is too fast
Reason:
During the baking process of castables, if the heating rate is too fast, the internal water evaporates quickly, and the steam pressure generated is large. When it exceeds the tensile strength of the castable, cracks will appear.
Solution:
Develop a reasonable baking curve and control the heating rate according to factors such as the type and thickness of the castable. Generally speaking, the initial heating stage should be slow, preferably not exceeding 50℃/h. As the temperature rises, the heating rate can be appropriately accelerated, but it should also be controlled at around 100℃/h - 150℃/h. During the baking process, use a temperature recorder to monitor temperature changes in real time to ensure that the heating rate meets the requirements.
2. Material quality problem
Reason:
Improper ratio of aggregate to powder: If there are too many aggregates and insufficient powder, the bonding performance of the castable will decrease, and cracks will easily appear during baking; on the contrary, too much powder will increase the shrinkage rate of the castable and also easily cause cracks.
Improper use of additives: The type and amount of additives have an important impact on the performance of the castable. For example, excessive use of water reducer may cause excessive fluidity of the castable, resulting in segregation during the solidification process, and cracks will appear during baking.
Solution:
Strictly control the quality of raw materials, and accurately weigh raw materials such as aggregates, powders and additives according to the formula requirements provided by the manufacturer. Regularly inspect and screen the raw materials to ensure that their particle size, gradation and chemical composition meet the requirements.
For new batches of raw materials, first conduct a small sample test to test the performance of the castable, such as fluidity, strength, shrinkage, etc., adjust the formula and additive dosage according to the test results, and then use them on a large scale after they are qualified.
3. Construction process problems
Reasons:
Uneven mixing: If the castable is not mixed evenly during mixing, the water and additives in it will be unevenly distributed, and cracks will occur during baking due to performance differences in different parts.
Uncompacted vibration: During the pouring process, uncompacted vibration will cause pores and voids inside the castable, and these weak parts are prone to cracks during baking.
Improper maintenance: If the water on the surface of the castable is not fully maintained after pouring, the water evaporates too quickly, which will cause excessive surface shrinkage and cracks.
Solution:
Use mechanical mixing and strictly control the mixing time. Generally speaking, the mixing time of a forced mixer is not less than 3-5 minutes to ensure that the castable is mixed evenly. During the mixing process, add an appropriate amount of water to make the castable reach the appropriate fluidity.
When vibrating, use appropriate vibrating tools, such as vibrating rods, etc., and vibrate in a certain order and spacing to ensure that the castable is dense. The vibration time is suitable for no bubbles and sinking on the surface of the castable.
After pouring, curing should be carried out in time. Plastic film, wet straw mats and other methods can be used to keep the surface of the castable moist, and the curing time is generally not less than 7-10 days. For large-volume castables or castables constructed in high-temperature environments, spray curing and other measures can also be taken.
4. Baking environment problem
Cause:
The ambient temperature is too low: When baking in a low-temperature environment, the solidification and drying speed of the castable is slow, and it is easy to be frozen, resulting in internal structural damage, thus cracking.
Poor ventilation: During the baking process, if the ventilation is not smooth, the water evaporated from the inside of the castable cannot be discharged in time, and accumulates inside to form high pressure, causing cracks.
Solution:
When the ambient temperature is lower than 5℃, heating measures should be taken, such as using a heater, steam pipe, etc. to preheat the baking environment, so that the ambient temperature rises to above 10℃-15℃ before baking. During the baking process, the ambient temperature should also be kept stable to avoid excessive temperature fluctuations.
Reasonably set the vents to ensure good ventilation during the baking process. According to the size and shape of the baking equipment, multiple vents can be set, and the size of the vents can be adjusted as needed to ensure that moisture can be discharged smoothly. At the same time, care should be taken to avoid placing castables directly at the vents to avoid cracks due to local air drying too quickly.
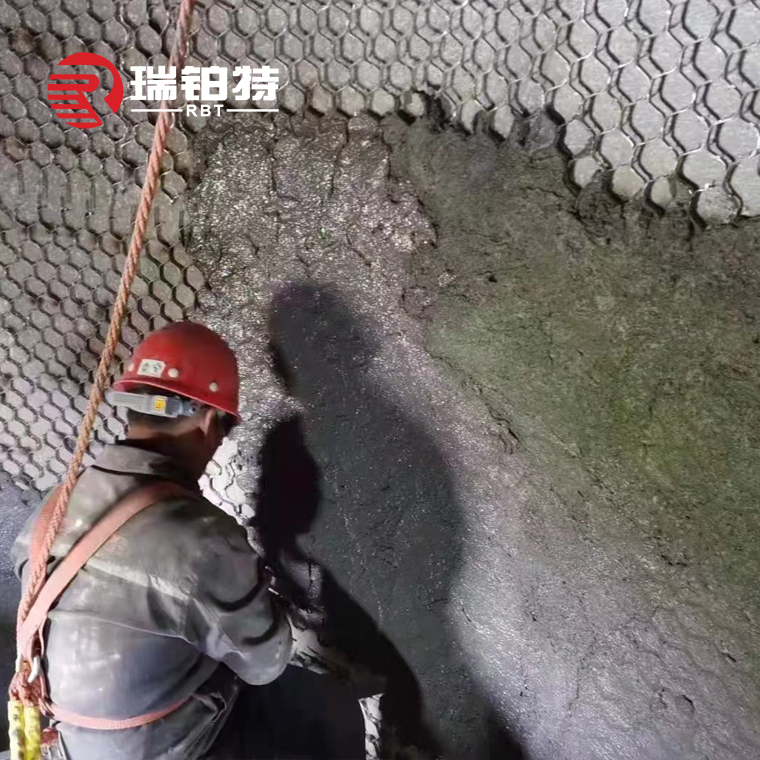
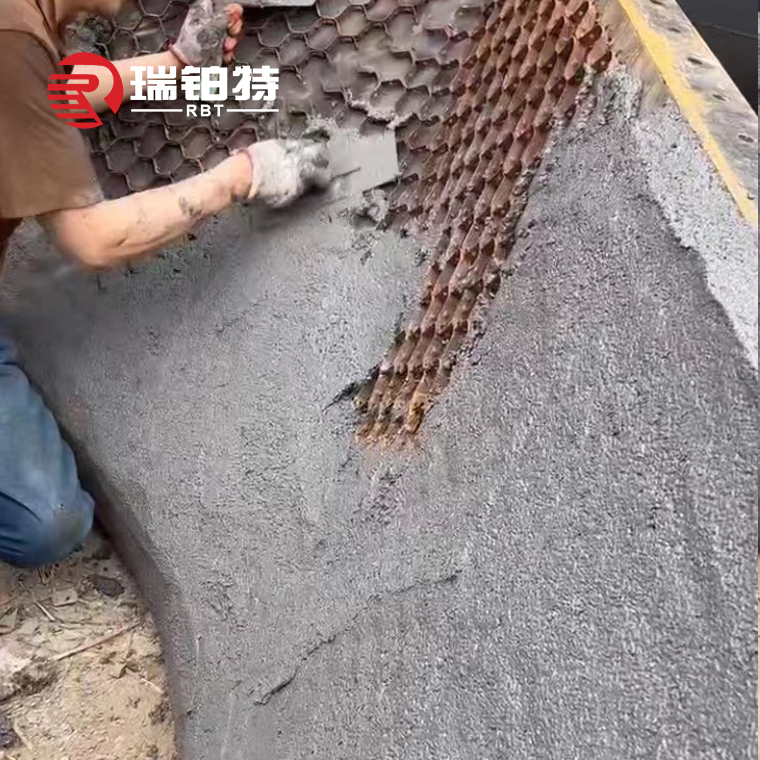
Post time: May-07-2025