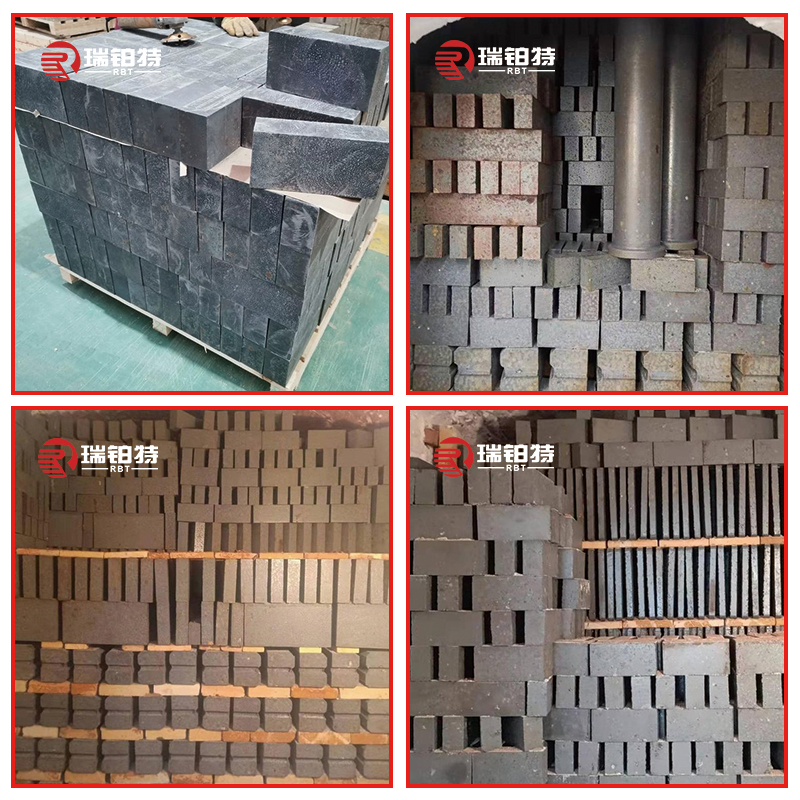
In the realm of modern industry, where high - temperature operations are the norm, the choice of refractory materials can significantly impact the efficiency, durability, and cost - effectiveness of production processes. Silicon carbide bricks have emerged as a leading solution, offering a unique combination of properties that make them indispensable in a wide range of applications.
Exceptional Physical and Chemical Properties
High Hardness and Abrasion Resistance
Silicon carbide bricks boast a remarkable Mohs hardness of 9, which is close to that of a diamond. This high hardness enables them to withstand severe abrasion from high - velocity particles, molten materials, and mechanical scrubbing. In industries such as mining, metallurgy, and cement production, where equipment is constantly exposed to abrasive substances, the use of silicon carbide bricks can greatly extend the service life of furnace linings, ducts, and other critical components. For example, in cement kilns, the abrasive nature of the raw materials and the high - temperature environment can cause rapid wear of traditional refractory materials. Silicon carbide bricks, with their outstanding abrasion resistance, can endure these harsh conditions, reducing the frequency of maintenance and replacement, and ultimately lowering production costs.
Outstanding Thermal Conductivity
One of the key features of silicon carbide bricks is their high thermal conductivity. This property allows for efficient heat transfer within industrial furnaces and reactors. In applications where rapid heating and cooling cycles are required, such as in the semiconductor manufacturing process for annealing and sintering, silicon carbide bricks can quickly transfer heat to the workpiece, ensuring uniform temperature distribution. As a result, the production process becomes more efficient, and the quality of the final product is improved. In addition, the high thermal conductivity of silicon carbide bricks also helps to reduce energy consumption. By enabling faster heat transfer, less energy is wasted in the form of heat loss, leading to significant savings in energy costs over time.
Excellent Thermal Stability
Silicon carbide bricks can maintain their structural integrity and mechanical properties at extremely high temperatures, up to 1800°C (3272°F) in some cases. This exceptional thermal stability makes them suitable for use in high - temperature furnaces, such as those used in the production of steel, non - ferrous metals, and glass. In a steel - making furnace, for instance, the lining needs to withstand the intense heat of molten steel and the continuous thermal cycling during the production process. Silicon carbide bricks can endure these conditions without significant deformation or degradation, providing reliable protection for the furnace shell and ensuring smooth production operations.
Superior Chemical Resistance
These bricks exhibit excellent resistance to both acidic and alkaline substances. In chemical industries, where corrosive chemicals are used in large quantities, silicon carbide bricks can be used to line reactors, storage tanks, and pipelines. They can effectively resist the corrosion of various acids, alkalis, and salts, preventing leaks and ensuring the safe operation of the equipment. For example, in the production of fertilizers, where strong acids and alkalis are involved in the manufacturing process, silicon carbide bricks offer long - lasting protection against chemical corrosion, reducing the risk of equipment failure and environmental pollution.
Diverse Applications Across Multiple Industries
1. Metallurgical Industry
Steelmaking: In the steel - making process, silicon carbide bricks are used in electric arc furnaces, ladles, and tundishes. Their high thermal conductivity helps in quickly heating and melting the steel, while their excellent resistance to molten steel and slag erosion ensures the longevity of the furnace lining. This not only improves the efficiency of steel production but also reduces the need for frequent relining, which is a time - consuming and costly process.
Non - ferrous Metal Smelting: For the smelting of metals such as aluminum, copper, and zinc, silicon carbide bricks are also widely applied. In aluminum smelting, for example, the bricks are used in electrolytic cells and holding furnaces. Their resistance to the corrosive effects of molten aluminum and its associated salts, along with their high thermal stability, makes them an ideal choice for maintaining the integrity of the smelting equipment and ensuring a consistent production process.
2. Ceramic and Glass Industry
Ceramic Manufacturing: In ceramic kilns, silicon carbide bricks are used as kiln furniture, including shelves, supports, and saggers. Their high strength at elevated temperatures allows them to bear the weight of ceramic products during firing, while their good thermal conductivity ensures uniform heating of the ceramics. This results in high - quality ceramic products with consistent color and texture. Moreover, the long service life of silicon carbide kiln furniture reduces the cost of replacement and downtime in ceramic production.
Glass Production: In glass furnaces, silicon carbide bricks are used in the areas where high - temperature and corrosive environments are present, such as the combustion chamber and the glass - melting zone. They can withstand the high - temperature molten glass and the corrosive action of glass - forming chemicals, providing reliable insulation and protection for the furnace structure. This helps to improve the efficiency of glass melting and the quality of the glass produced.
Power Generation and Waste Incineration.
Power Plants: In coal - fired power plants, silicon carbide bricks are used in boilers and ash - handling systems. They can resist the abrasion of fly ash and the high - temperature combustion environment, enhancing the reliability and efficiency of power generation equipment. In addition, in biomass - fired power plants, where the combustion of biomass produces corrosive gases and ash, silicon carbide bricks offer excellent resistance to these harsh conditions, ensuring the stable operation of the power plant.
Waste Incineration Plants: Waste incineration involves high - temperature combustion of various waste materials, which can produce highly corrosive gases and ash. Silicon carbide bricks are used in the lining of incinerators to withstand these extreme conditions. Their chemical resistance protects the incinerator walls from corrosion, while their high - temperature stability ensures the safe and efficient operation of the waste incineration process.
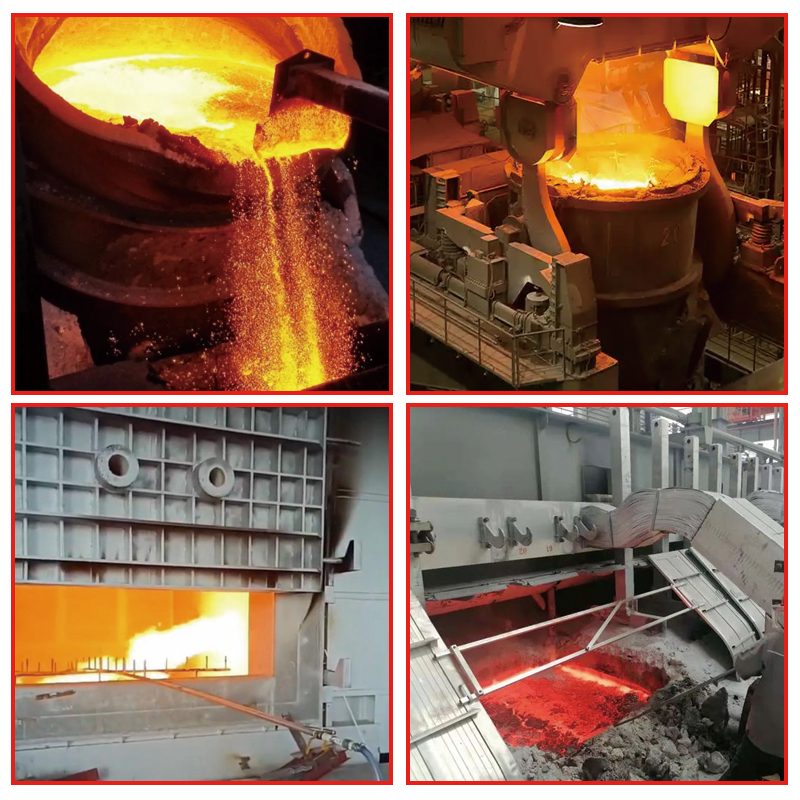
Choosing the Right Silicon Carbide Bricks for Your Needs
When selecting silicon carbide bricks for your industrial application, several factors need to be considered:
Purity and Composition
The purity of silicon carbide in the bricks affects their performance. Higher - purity silicon carbide bricks generally offer better thermal conductivity, chemical resistance, and mechanical strength. For applications where extreme conditions are present, such as in high - temperature, highly corrosive environments, high - purity silicon carbide bricks are recommended. Additionally, the type of binder used in the brick manufacturing process can also impact its properties. Different binders, such as clay, nitride, or sialon, provide different levels of strength, thermal shock resistance, and chemical resistance.
Manufacturing Process and Quality Control
Choose bricks that are manufactured using advanced and reliable processes. A well - controlled manufacturing process ensures consistent quality in terms of brick dimensions, density, and mechanical properties. Look for manufacturers who adhere to international quality standards, such as ISO 9001. Quality control measures, including strict inspection of raw materials, in - process monitoring, and final product testing, are essential to ensure that the silicon carbide bricks meet the required specifications.
Customization Options
Depending on your specific application, you may require silicon carbide bricks in non-standard shapes or sizes. As a manufacturer, Robert can offer customization services to meet your unique needs. Custom-made bricks can be designed to fit precisely into your equipment, optimizing their performance and ensuring a perfect fit in your industrial setup. In conclusion, silicon carbide bricks are a versatile and high - performance refractory material that can significantly enhance the efficiency and durability of industrial operations. Whether you are in the metallurgical, ceramic, glass, power generation, or waste incineration industry, considering silicon carbide bricks for your high - temperature applications can lead to substantial savings in terms of maintenance, energy consumption, and production downtime. Explore the possibilities of silicon carbide bricks today and take your industrial processes to the next level of excellence.
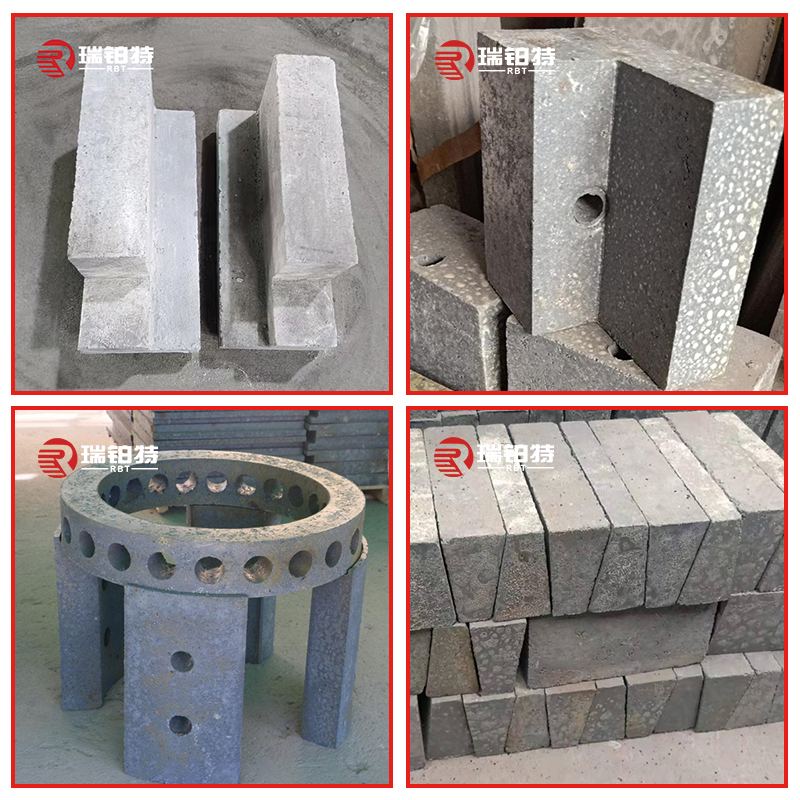
Post time: Jul-09-2025