1. Red kiln brick falling
Cause:
(1) When the rotary kiln skin is not well hung.
(2) The cylinder is overheated and deformed, and the inner wall is uneven.
(3) The kiln lining is not of high quality or is not replaced on schedule after being worn thin.
(4) The center line of the rotary kiln cylinder is not straight; the wheel belt and the pad are seriously worn, and the radial deformation of the cylinder increases when the gap is too large.
Troubleshooting method:
(1) The batching work and calcination operation can be strengthened.
(2) Strictly control the gap between the wheel belt and the pad near the firing zone. When the gap is too large, the pad should be replaced in time or adjusted with pads. In order to prevent and reduce the wear caused by long-term movement between the pads, lubricant should be added between the wheel belt and the pad.
(3) Make sure that the kiln is stopped when in operation, and repair or replace the cylinder of the rotary kiln with excessive deformation in time;
(4) Regularly calibrate the center line of the cylinder and adjust the position of the supporting wheel;
(5) Select high-quality kiln linings, improve the quality of inlay, strictly control the use cycle of kiln linings, check the brick thickness in time, and replace worn kiln linings in time.
2. The shaft of the supporting wheel is broken
Causes:
(1) The matching between the supporting wheel and the shaft is unreasonable. The interference fit between the supporting wheel and the shaft is generally 0.6 to 1/1000 of the shaft diameter to ensure that the supporting wheel and the shaft will not loosen. However, this interference fit will cause the shaft to shrink at the end of the supporting wheel hole, resulting in stress concentration. It is not difficult to imagine that the shaft will break here, and this is the case.
(2) Fatigue fracture. Due to the complex force of the supporting wheel, if the supporting wheel and the shaft are considered as a whole, the bending stress and shear stress of the shaft are the largest at the corresponding part of the end of the supporting wheel hole. This part is prone to fatigue under the action of alternating loads, so the fracture should also occur at the end of the joint between the supporting wheel and the shaft.
(3) Manufacturing defects The roller shaft generally needs to be forged, machined, and heat treated by steel ingots or round steel. Once defects occur in the middle and are not detected, such as impurities in the steel ingot, forging insect skin, etc., and micro cracks appear during heat treatment. These defects not only limit the bearing capacity of the shaft, but also cause stress concentration. As a source, once the crack expands, fracture is inevitable.
(4) Temperature stress or improper force The heating of the large tile of the rotary kiln is a common fault. If the operation and maintenance are improper, it is easy to cause surface cracks on the roller shaft. When the large tile heats up, the temperature of the shaft must be very high. At this time, if the shaft is cooled rapidly, due to the slow internal cooling of the shaft, the rapidly shrinking shaft surface can only release the huge shrinkage stress through cracks. At this time, the surface cracks will produce stress concentration. Under the action of alternating stress, once the crack expands circumferentially and reaches a certain degree, it will break. The same is true for the excessive force on the roller. For example, improper adjustment causes excessive force on the shaft or a certain section of the shaft, which is easy to cause the fracture of the roller shaft.
Exclusion method:
(1) Different interference amounts are used in the supporting wheel and shaft inclusion area. Because the interference amount between the supporting wheel and the shaft is large, the shaft will shrink at this place after the end of the inner hole of the supporting wheel is hot-fitted, cooled and tightened, and the stress concentration is too large. Therefore, during the design, manufacturing and installation process, the interference amount of the two ends of the inner hole of the supporting wheel (range of about 100mm) is gradually reduced from the inside to the outside to alleviate the occurrence of necking. The reduction amount can be gradually reduced to one-third to one-half of the middle interference amount, so as to avoid or reduce the necking phenomenon.
(2) Comprehensive flaw detection to eliminate defects. Defects will reduce the bearing capacity of the shaft and cause stress concentration, which often causes fracture accidents. The harm is great and must be taken seriously. For the supporting wheel shaft, defects must be found in advance. For example, before processing, the material selection must be inspected and no problem materials must be selected; flaw detection must also be carried out during processing to eliminate defects, ensure the internal quality of the shaft, and at the same time ensure the processing accuracy of the shaft, and eliminate crack sources and stress concentration sources.
(3) Reasonable adjustment of the kiln to reduce additional loads. Multiple roller shafts support the entire weight of the kiln through the rollers. The load is very large. If the installation or maintenance adjustment is improper, eccentric load will occur. When the distance from the center line of the kiln is inconsistent, a certain roller will be subjected to excessive force; when the axis of the roller is not parallel to the center line of the kiln, the force on one side of the shaft will increase. Improper excessive force will cause the large bearing to heat up, and will also cause damage to the shaft due to the large stress at a certain point of the shaft. Therefore, the maintenance and adjustment of the kiln must be taken seriously to avoid or reduce additional loads and make the kiln run lightly. During the maintenance process, avoid starting fire and welding on the shaft, and avoid grinding the shaft with a grinding wheel to reduce damage to the shaft.
(4) Do not cool the hot shaft rapidly during operation. During the operation of the kiln, the large bearing will cause heating due to some reasons. At this time, in order to reduce production losses, some units often adopt rapid cooling, which is easy to cause micro cracks on the surface of the shaft, so slow cooling should be adopted to avoid rapid cooling.
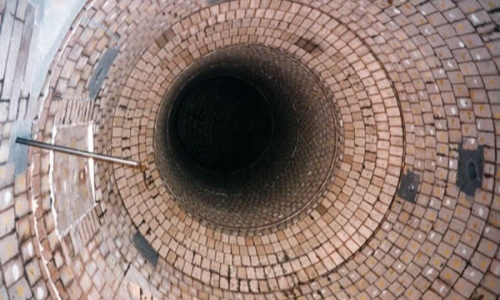
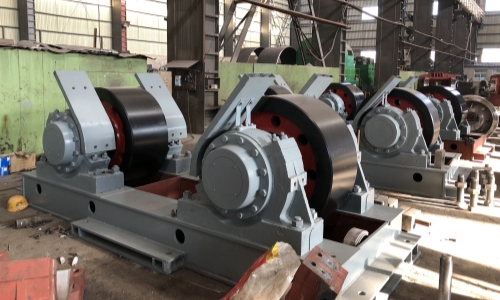
Post time: May-12-2025