In general, high aluminum bricks should not be used in the alkaline atmosphere furnace. Because the alkaline and acidic medium also have chlorine, it will penetrate the deep layers of high alumina bricks in the form of gradient, which will cause the refractory brick to collapse.
The high aluminum brick after the erosion of the alkaline atmosphere is horizontal cracks. The erosion is composed of fuel gray, burning gases, and alkaline components in other products. These components react with the glass phase and mullite stone in the high aluminum brick.
High-aluminum bricks that are corroded alkaline will appear on the surface. Burning gas compounds will also generate lure nitrate, sedimentation in the gap of high aluminum bricks; the reaction of the generated glaciers will form a complex new phase. When the water -free lucky nitriles are in contact with the generated vagram, the anti -vaporization reaction will occur, causing the high aluminum brick to crack or drop. In addition, thermal corrosion is also very serious for refractory brick corrosion. Because of the erosion of Fang quartz, Skywine, and quartz crystal silica. The use of fire tiles will be more serious than cold noodles.
The damage to the bricks of the silicon dioxide is also very serious. The silica is dissolved in high aluminum brick -liquid phase. The melting lucky nitrate and low -melting point silicon stones form a large amount of liquid phase. The higher the silica content in the brick, the greater the amount of liquid phase. Excessive liquid phases will deform high aluminum bricks. Silicon silicon is also damaged to bricks. Because the free silica is consumed, Mo Lai Shi phase will be eroded. After the response of the lickle nitrate and mullite stone can cause destructive expansion of the high aluminum brick.
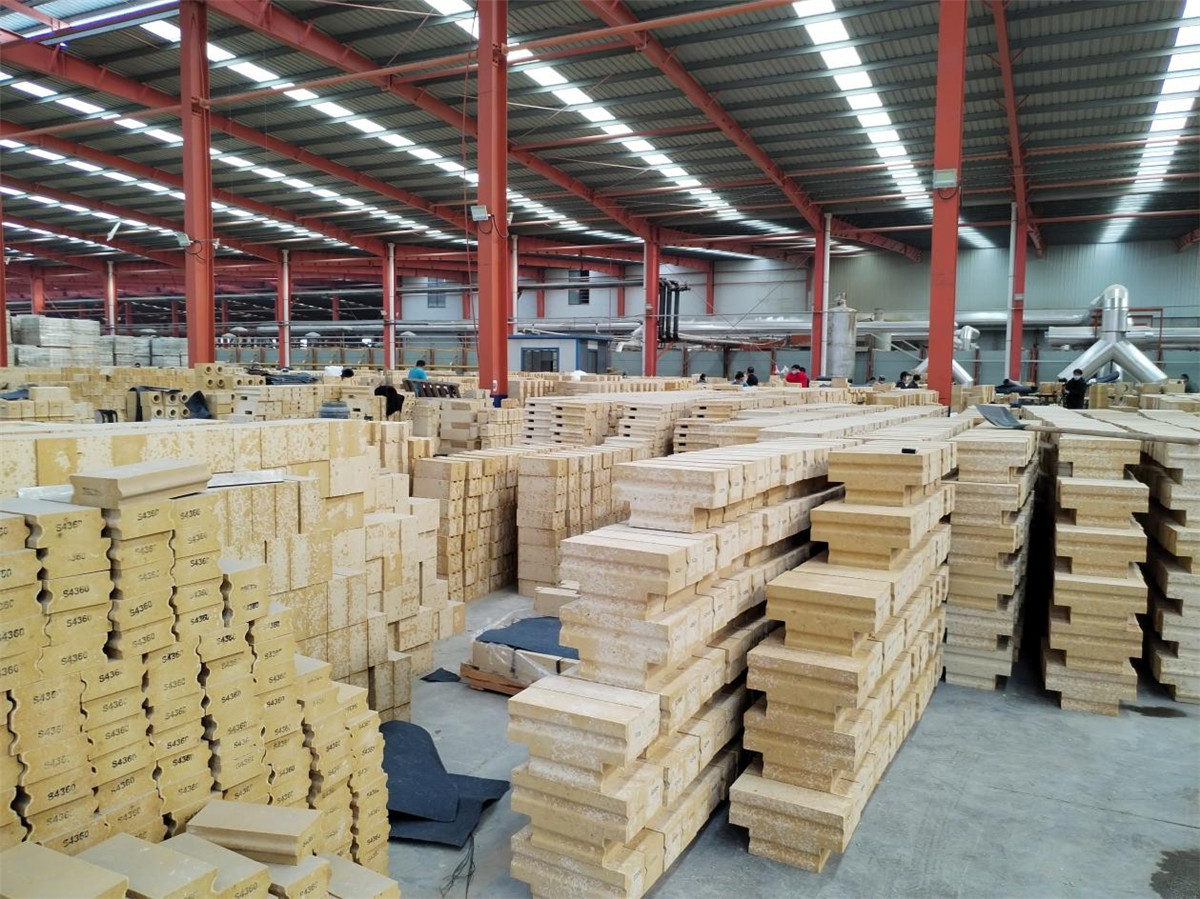
High aluminum bricks have excellent resistance to high temperature and abrasion. They are widely used in the lining of various industrial furnaces, such as blast furnaces, hot air furnaces, and rotary kilns. However, in the alkaline atmosphere industrial furnace, the use of high alumina bricks is limited.
The chemical properties of high alumina bricks make them resist the effects of acidic environments. However, in a highly alkaline environment, such as cement kilns or glass furnaces, high aluminum bricks will react with alkali metal oxides, causing the bricks to crack and disintegrate. The reaction between the Al2O3 bricks and the alkali metal oxides usually results in the formation of an alkali aluminosilicate gel, which has a low melting point and can easily flow through the cracks.
To solve this problem, several strategies have been applied to improve the resistance of high aluminum bricks to alkaline environments. One solution is to add magnesia or spinel to the high alumina bricks. The magnesia or spinel will react with the alkali metal oxides to form stable spinel phases, which can enhance the resistance of Al2O3 bricks to cracking caused by alkali reaction. Another solution is to apply a protective coating on the surface of the high alumina bricks to prevent direct contact with the alkaline environment.
In summary, high aluminum bricks have a limited applicability in alkaline atmosphere industrial furnace lining. To enhance the resistance of Al2O3 bricks in alkaline environments, it is necessary to add certain minerals or coatings to avoid harmful reactions with alkali metal oxides. It's crucial to select the right material for industrial furnace lining to reduce potential hazards and save costs.
Post time: May-19-2023