Low cement refractory castables are compared to traditional aluminate cement refractory castables. The cement addition amount of traditional aluminate cement refractory castables is usually 12-20%, and the water addition amount is generally 9-13%. Due to the high amount of water added, the cast body has many pores, is not dense, and has low strength; due to the large amount of cement added, although higher normal and low temperature strengths can be obtained, the strength decreases due to the crystalline transformation of calcium aluminate at medium temperatures. Obviously, the introduced CaO reacts with SiO2 and Al2O3 in the castable to generate some low-melting point substances, resulting in the deterioration of the material's high-temperature properties.
When ultrafine powder technology, high-efficiency admixtures and scientific particle gradation are used, the cement content of the castable is reduced to less than 8% and the water content is reduced to ≤7%, and a low-cement series refractory castable can be prepared and brought into The CaO content is ≤2.5%, and its performance indicators generally exceed those of aluminate cement refractory castables. This type of refractory castable has good thixotropy, that is, the mixed material has a certain shape and starts to flow with a little external force. When the external force is removed, it maintains the obtained shape. Therefore, it is also called thixotropic refractory castable. Self-flowing refractory castable is also called thixotropic refractory castable. Belongs to this category. The precise meaning of low cement series refractory castables has not been defined so far. The American Society for Testing and Materials (ASTM) defines and classifies refractory castables based on their CaO content.
Dense and high strength are the outstanding features of the low-cement series refractory castables. This is good for improving the service life and performance of the product, but it also brings troubles to baking before use, that is, pouring can easily occur if you are not careful during baking. The phenomenon of body bursting may require re-pouring at the least, or may endanger the personal safety of surrounding workers in severe cases. Therefore, various countries have also conducted various studies on the baking of low-cement series refractory castables. The main technical measures are: by formulating reasonable oven curves and introducing excellent anti-explosion agents, etc., this can make the refractory castables Water is eliminated smoothly without causing other side effects.
Ultrafine powder technology is the key technology for low-cement series refractory castables (currently most of the ultrafine powders used in ceramics and refractory materials are actually between 0.1 and 10m, and they mainly function as dispersion accelerators and structural densifiers. .The former makes the cement particles highly dispersed without flocculation, while the latter makes the micropores in the pouring body fully filled and improves the strength.
Currently commonly used types of ultrafine powders include SiO2, α-Al2O3, Cr2O3, etc. The specific surface area of SiO2 micropowder is about 20m2/g, and its particle size is about 1/100 of the cement particle size, so it has good filling properties. In addition, SiO2, Al2O3, Cr2O3 micropowder, etc. can also form colloidal particles in water. When a dispersant is present, an overlapping electric double layer is formed on the surface of the particles to generate electrostatic repulsion, which overcomes the van der Waals force between particles and reduces the interface energy. It prevents adsorption and flocculation between particles; at the same time, the dispersant is adsorbed around the particles to form a solvent layer, which also increases the fluidity of the castable. This is also one of the mechanisms of ultrafine powder, that is, adding ultrafine powder and appropriate dispersants can reduce the water consumption of refractory castables and improve fluidity.
The setting and hardening of low-cement refractory castables is the result of the combined action of hydration bonding and cohesion bonding. The hydration and hardening of calcium aluminate cement are mainly the hydration of the hydraulic phases CA and CA2 and the crystal growth process of their hydrates, that is, they react with water to form hexagonal flake or needle-shaped CAH10, C2AH8 and Hydration products such as cubic C3AH6 crystals and Al2O3аq gels then form an interconnected condensation-crystallization network structure during the curing and heating processes. The agglomeration and bonding is due to the active SiO2 ultrafine powder forming colloidal particles when it meets water, and meets the ions slowly dissociated from the added additive (i.e. electrolyte substance). Because the surface charges of the two are opposite, that is, the colloid surface has adsorbed counter ions, causing the £2 The potential decreases and condensation occurs when adsorption reaches the "isoelectric point". In other words, when the electrostatic repulsion on the surface of the colloidal particles is less than its attraction, cohesive bonding occurs with the help of van der Waals force. After the refractory castable mixed with silica powder is condensed, the Si-OH groups formed on the surface of SiO2 are dried and dehydrated to bridge, forming a siloxane (Si-O-Si) network structure, thereby hardening. In the siloxane network structure, the bonds between silicon and oxygen do not decrease as the temperature increases, so the strength also continues to increase. At the same time, at high temperatures, the SiO2 network structure will react with the Al2O3 wrapped in it to form mullite, which can improve the strength at medium and high temperatures.
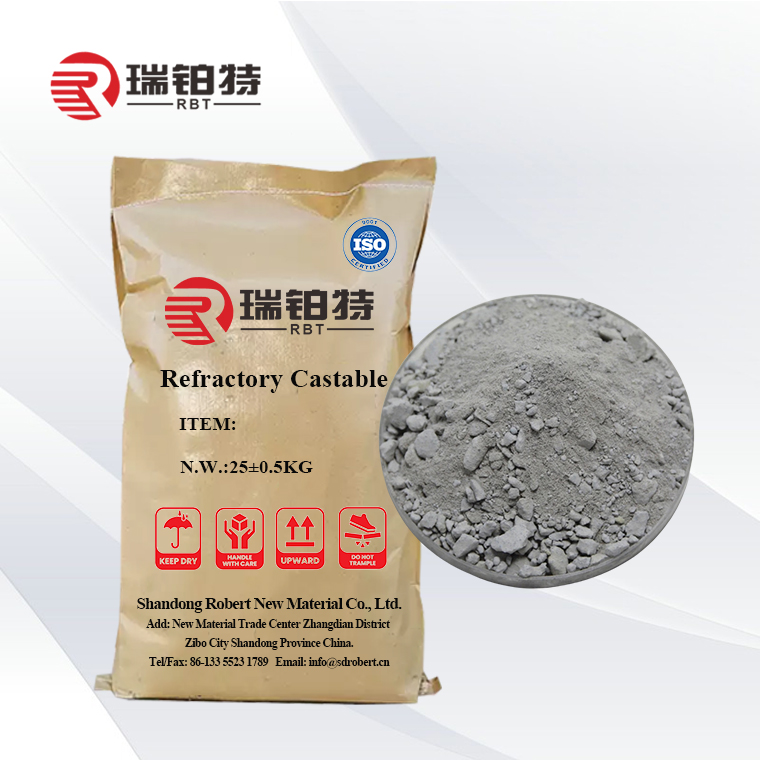
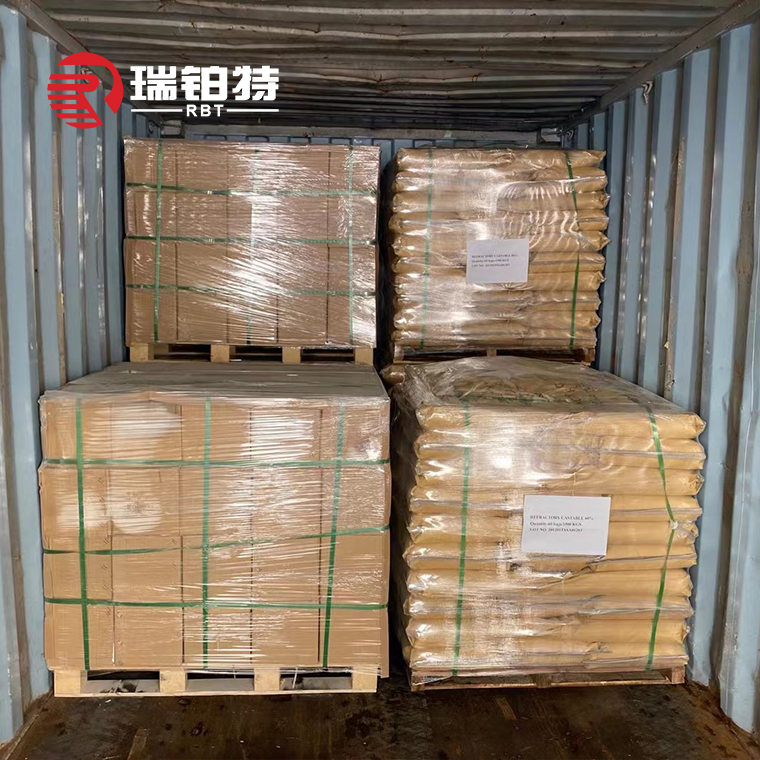
Post time: Feb-28-2024