The advantages of magnesia carbon bricks are: resistance to slag erosion and good thermal shock resistance. In the past, the disadvantage of MgO-Cr2O3 bricks and dolomite bricks was that they absorbed slag components, resulting in structural spalling, leading to premature damage. By adding graphite, magnesia carbon bricks eliminated this shortcoming. Its characteristic is that the slag only penetrates into the working surface, so the reaction layer Confined to the working surface, the structure has less peeling and a long service life.
Now, in addition to traditional asphalt and resin-bonded magnesia carbon bricks (including fired oil-impregnated magnesia bricks), the magnesia carbon bricks sold on the market include:
(1) Magnesia carbon bricks made of magnesia containing 96%~97% MgO and graphite 94%~95%C;
(2) Magnesia carbon bricks made of magnesia containing 97.5% ~ 98.5% MgO and graphite 96% ~ 97% C;
(3) Magnesia carbon bricks made of magnesia containing 98.5%~99% MgO and 98%~C graphite.
According to the carbon content, magnesia carbon bricks are divided into:
(I) Fired oil-impregnated magnesia bricks (carbon content less than 2%);
(2) Carbon bonded magnesia bricks (carbon content less than 7%);
(3) Synthetic resin bonded magnesia carbon brick (carbon content is 8%~20%, up to 25% in a few cases). Antioxidants are often added to asphalt/resin bonded magnesia carbon bricks (carbon content is 8% to 20%).
Magnesia carbon bricks are produced by combining high-purity MgO sand with scaly graphite, carbon black, etc. The manufacturing process includes the following processes: raw material crushing, screening, grading, mixing according to material formula design and product setting performance, according to the combination The temperature of the agent type is raised to close to 100~200℃, and it is kneaded together with the binder to obtain the so-called MgO-C mud (green body mixture). The MgO-C mud material using synthetic resin (mainly phenolic resin) is molded in a cold state; the MgO-C mud material combined with asphalt (heated to a fluid state) is molded in a hot state (at about 100°C) forming. According to the batch size and performance requirements of MgO-C products, vacuum vibration equipment, compression molding equipment, extruders, isostatic presses, hot presses, heating equipment, and ramming equipment can be used to process MgO-C mud materials. to the ideal shape. The formed MgO-C body is placed in a kiln at 700~1200°C for heat treatment to convert the binding agent into carbon (this process is called carbonization). In order to increase the density of magnesia carbon bricks and strengthen the bonding, fillers similar to binders can also be used to impregnate the bricks.
Nowadays, synthetic resin (especially phenolic resin) is mostly used as the binding agent of magnesia carbon bricks. The use of synthetic resin bonded magnesia carbon bricks has the following basic advantages:
(1) Environmental aspects allow the processing and production of these products;
(2) The process of producing products under cold mixing conditions saves energy;
(3) The product can be processed under non-curing conditions;
(4) Compared with tar asphalt binder, there is no plastic phase;
(5) Increased carbon content (more graphite or bituminous coal) can improve wear resistance and slag resistance.
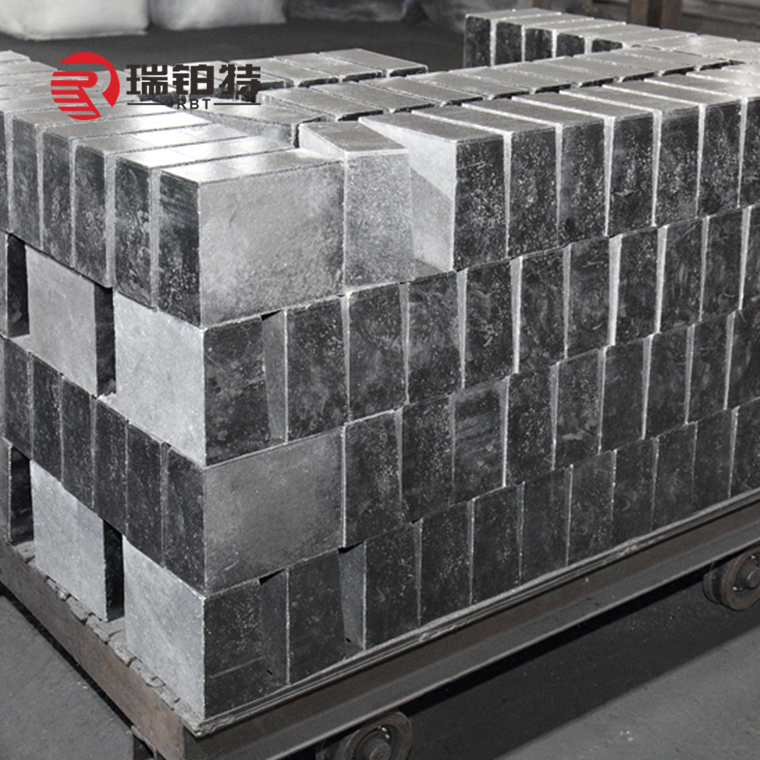
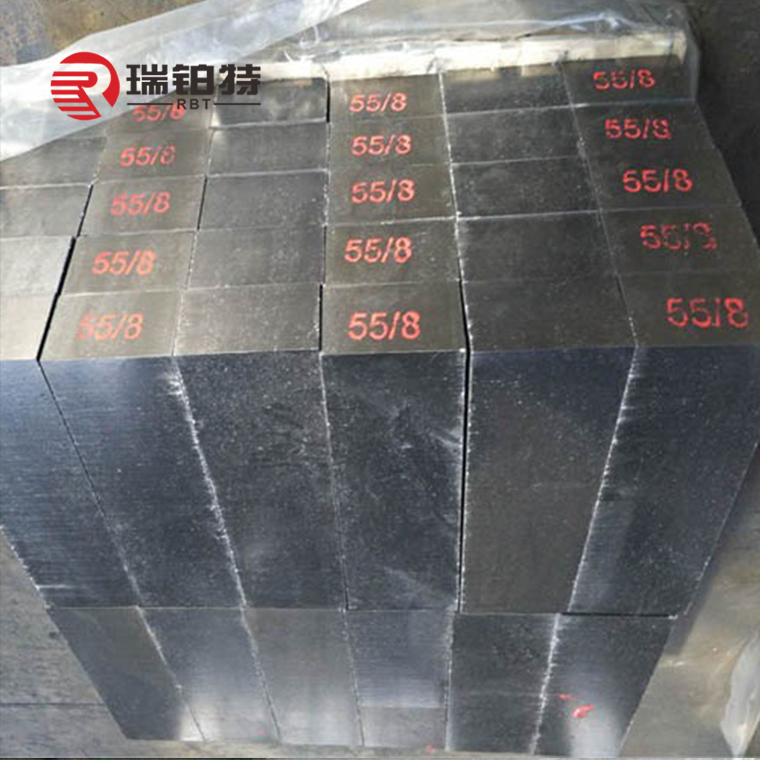
Post time: Feb-23-2024